多层级超级BoMs¶
Use a multilevel bill of materials (BoM) when a manufactured product is part of another assembly. This method nests BoMs within other BoMs, organizing complex products while simplifying manufacturing by defining each procurement and production step separately.
Sublevel BoMs (subassemblies or semifinished products) streamline these production workflows, and are beneficial when the subassembly is used across multiple finished products (meaning they’d appear on multiple top-level BoMs). The more complicated a product is to build or procure, the more value a multilevel BoM can provide. Because of this, component and subassembly replenishment planning is vital to ensuring multilevel BoMs run smoothly.
Why replenishment planning is important¶
Replenishment is critical for multilevel BoMs to prevent bottlenecks, manage lead times, and optimize inventory. Without it, missing components can halt production, delay orders, and increase costs. A well-planned replenishment strategy ensures just-in-time availability, automates procurement, balances stock levels, and keeps supply chains efficient. This minimizes delays, reduces manual effort, and ensures smooth manufacturing.
Manufacturing orders (MO)s that come from a BoM require all components to be available before the MO can be completed. The Component Status for that MO provides this information. Learn how to check an MO’s component status.
Create a multilevel BoM¶
To set up a multilevel BoM, the top-level product and sublevel products’s BoMs must be created. If starting from scratch, build the BoMs from the bottom up. Start with the lowest-level product BoMs, then include those products as components in higher-level BoMs.
Example
A printed circuit board (PCB) for a custom keyboard is composed of hundreds of electronic
components, such as transistors, resistors, and capacitors. Instead of listing all of those
components out, a sublevel product and BoM for a PCB
is created, to track the quantities of
transistors and other small components, without needing to overcrowd the top-level BoM for the
custom keyboard by listing them. Instead, the custom keyboard’s BoM consists of an assortment
of components and sublevel BoMs alike, like key caps, switches, the PCB, and keyboard plate.
Learn how to build a simple bill of materials. For the PCB, this would include the transistors, resistors, and other components.
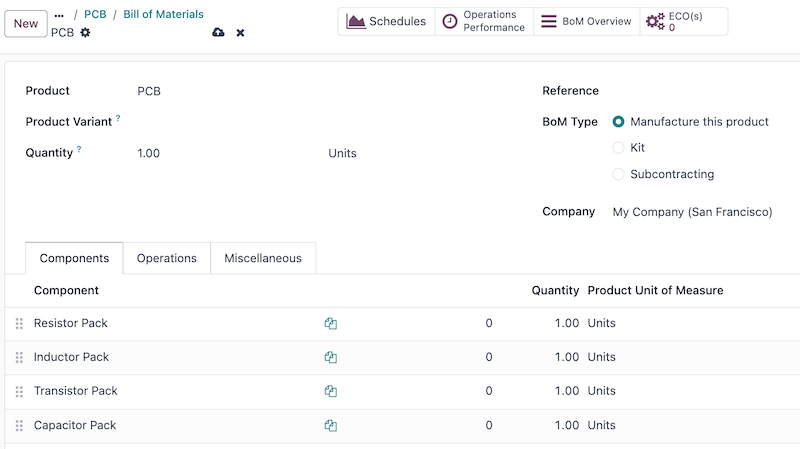
After the sublevel products (like the PCB, key caps, and keyboard plate) are fully configured, create the top-level product by navigating to New. From here, configure the product’s specifications as needed.
, and then selectingOnce the top-level product (the keyboard) is configured, click the Bill of Materials smart button on the product form, and then select New to make a BoM for the top-level product. Add the sublevel products to this BoM, along with any other necessary components.

管理生产计划¶
The two options below are two of the best ways to manage manufacturing order automation for products with multilevel BoMs.
注解
Complex BoMs are specifically used to manage products that require manufactured components. If a BoM is being created to organize components or bundle sellable products, use a kit instead.
To automatically trigger manufacturing orders for sublevel products after confirming a manufacturing order for the main product, there are two options:
Option 1 (recommended): Create Reordering Rules for the sublevel products and set both the minimum and maximum needed stock quantities to
0
.Option 2: Activate the Replenish on Order (MTO) and Manufacture routes under the Inventory tab of the sublevel product’s product form.
更多内容
Option 1 is more flexible than Option 2 and is recommended. Reordering rules do not directly link demand to replenishment, allowing stock to be unreserved and reassigned as needed. The Replenish on Order (MTO) route, however, uniquely links sublevel and top-level products, reserving quantities for the confirmed top-level manufacturing order.
In both methods, sublevel products must be fully manufactured before starting the top-level product.
Multilevel BoM setup flow¶
The following section details how to set up multilevel BoMs, set the initial inventory, establish a 0/0/1 reordering rule (the recommended production plan), configure lead times, and set up production options.
Creating a 0/0/1 reordering rule for the sublevel products (minimum stock set at zero, maximum stock set at zero, reorder one automatically) regardless of whether they are a component or subassembly is the recommended approach for managing a multilevel BoM. This setup uses the Inventory, Manufacturing, and Purchase apps.
重要
This is only one example of how to set up a multilevel BoM in Odoo. Consider any unique circumstances that need to be addressed during the configuration, and make sure they are included in the setup. If any specific help is needed during setup, consider purchasing a success pack.
Create the BoMs¶
Follow the steps in the Create a multilevel BoM section to build the BoMs.
Make sure to build the multilevel BoM from the bottom up. Start by creating the lowest-level component products in Odoo, then the subassembly products that those are used for, then the BoM for that subassembly, and repeat until every level of the multilevel BoM is created.
Set the initial inventory¶
注解
If there’s no initial inventory to configure, then skip this section and begin configuring the procurement method for the multilevel BoM.
Update the quantity on hand for each of the products configured in the prior step (both components, subassemblies, and the final product). To do this, open the Inventory app, and then find the products with filters, the search bar, or scrolling, and then click on them to open their product form. From here, click the On Hand smart button, select the variant if that was configured, and then enter the quantity on hand.
更多内容
Configure the procurement method¶
Now it is time to pick the procurement method this multilevel BoM uses. The two options below are preferred, but unique circumstances may lead to another procurement method making more sense.
Option 1 (recommended): Create Reordering Rules for the sublevel products and set both the minimum and maximum needed stock quantities to
0
.Option 2: Activate the Replenish on Order (MTO) and Manufacture routes under the Inventory tab of the sublevel product’s product form.
更多内容
Reordering rules are recommended because they do not tie the manufactured product to a specific sales order, allowing that manufactured product to fulfill a different sales order if the original gets cancelled.
Making the product to order is not recommended because the manufactured product cannot be used to fulfill another sales order. However, this could be helpful if strict tracking is necessary for the business.
Enter vendor and manufacturing lead times¶
Vendor and manufacturing lead times are used by Odoo to coordinate production and procurement actions to fulfill orders on time. Set vendor lead times for components that are purchased. These can appear at any level in a multilevel BoM except the final product. Set manufacturing lead times for products that are built using a BoM. These can appear at any level in a multilevel BoM except the lowest level (when individual components are procured).
更多内容
Build out operations to handle the production flow¶
First, determine the current manufacturing flow for the business, then match the corresponding Odoo setup. The list below are only some of the configuration pieces that could be involved in this step.
Manufacturing Steps: Consider how many manufacturing steps are taken (one-, two-, or three-step manufacturing).
Work Centers: Decide if any work centers need to be configured.
Master Production Schedule: If manually planned manufacturing orders are needed (e.g., to handle seasonal demand), make a master production schedule (MPS).
小技巧
Manufacturing operations is an art and a science, so configuring an established flow into Odoo is the recommended approach for this step. Read more about manufacturing in Odoo
Configuration summary¶
At the end of this process, the multilevel BoM is configured, and the top-level product has its inventory counts, procurement method set, procurement lead times, and manufacturing operations configured. From here, sales orders can include the top-level product, automatic procurement through vendors or manufacturing can begin, the top-level product can be included in an eCommerce store.
更多内容